As its team of aerospace heavyweights continues to grow, aircraft developer Aerion Supersonic has unveiled a finalized design for the AS2 business jet, which it believes is not only sustainable but also lays a solid foundation for a follow-on family of high-speed commercial and military derivatives.
Notwithstanding the devastating impact of the COVID-19 pandemic on air travel in 2020, Aerion believes the appetite for reduced journey times and enhanced global mobility will inevitably return in a post-pandemic world. Regardless of whether this happens sooner or later, the company acknowledges that long-term market acceptance of the AS2 still hinges on achieving environmental sustainability, both in terms of noise and emissions.
First unveiled by founder Robert Bass in 2004, the year after the retirement of the Anglo-French Concorde, the initial Aerion configuration was designed to operate in a new market niche below that Mach 2.2 airliner. Targeted at supersonic speeds over water, it was also tailored for efficient high subsonic, or transonic, flight around Mach 0.96 over land where, in most countries, no sonic boom is allowed.
To fill this hitherto untapped market, the configuration employed a novel wing design shaped for passive supersonic natural laminar flow (SNLF)—a condition in which the boundary layer flow remains stable for longer before becoming turbulent and causing friction drag. The technology was championed by aerodynamicist Richard Tracy—-Aerion’s co-founder and chief technology officer—who believed the low-drag, low-aspect-ratio shape would permit the aircraft to fly with limited transonic drag penalty at high subsonic speed over land and, where permitted, supersonically up to Mach 1.6.
Initial development focused on thin wing profiles in which shaping, rather than active control systems such as suction, could stabilize the boundary layer through pressure distribution. Encouraged by flight-test results of a scaled wing section with NASA in 2010, Aerion estimated the SNLF wing would have 20% less drag than a conventional delta wing and contended that increasing laminar flow fraction could lead to significant weight savings.
Although the overall design morphed from a twinjet to a trijet in 2014 as takeoff and landing noise considerations became a bigger factor, the configuration—by then called the AS2—retained its unusual trapezoidal wing as Aerion went through partnerships with Airbus and, in 2017, Lockheed Martin. The same basic wing shape, though now supporting engines slung under the wing and mounted on the upper fuselage, also continued as a feature until recently, well after the company’s pivotal new partnership with Boeing.
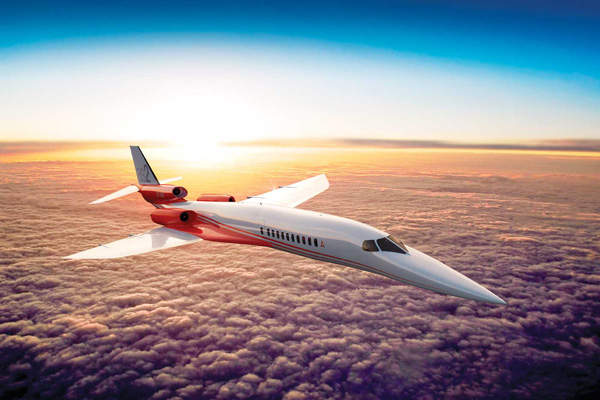
The teaming with Boeing, unveiled in February 2019 just a few months after Aerion signed up GE (GE Aviation) as engine supplier with the Affinity, helped dramatically accelerate the AS2 project. In addition to Boeing, which will support engineering, manufacturing and flight testing, a raft of other partners and suppliers have joined the program. These notably include Honeywell, which is providing the avionics, and Safran for landing gear and nacelles. UK-based GKN Aerospace and Fokker Technologies, which that company acquired in 2015, are providing electrical wiring and the empennage structure. Spirit AeroSystems will supply the forward fuselage.
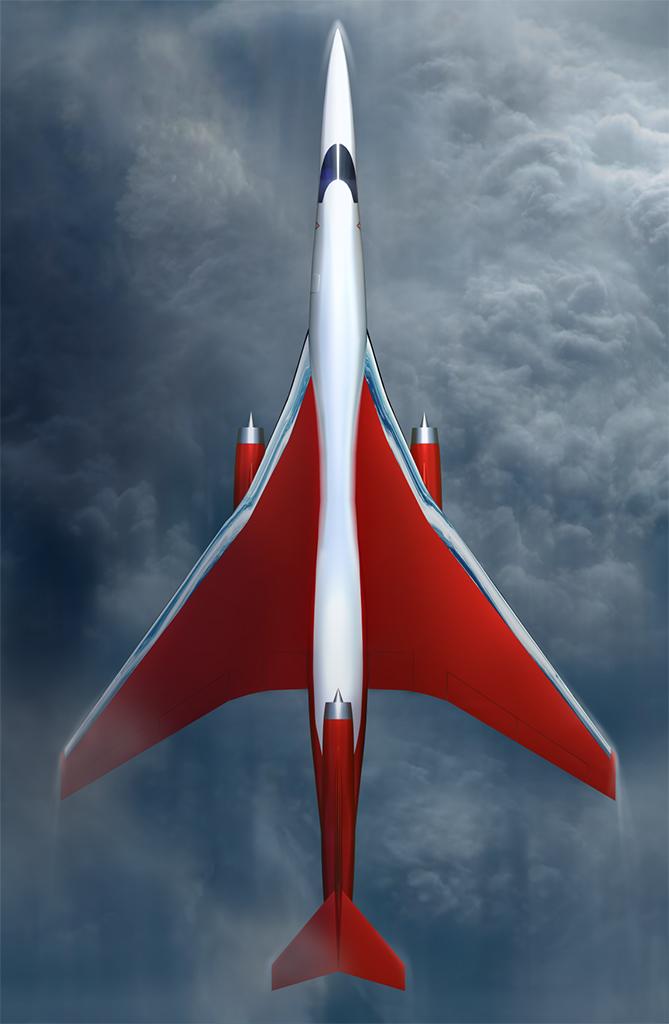
The latest design update also reflects Aerion’s decision to increase the AS2’s overland speed capability with a technique it calls boomless cruise. With competition stirring, including potential low-boom designs that in the future may build on technology being tested in NASA’s X-59 demonstrator program, the company is keen to make the AS2 equally attractive for transcontinental as well as transoceanic missions. Aerion therefore aims to offer a boomless cruise capability up to around Mach 1.2 by exploiting the Mach cutoff phenomenon in which thicker air at lower altitude refracts the boom away from the ground under particular atmospheric conditions.
The 79-ft.-span wing has large actuated leading and trailing edges for improved low-speed flight and field performance—an important factor for meeting noise regulations with reduced engine power for takeoff. Although no details are being given about the movable surfaces, the trailing edge is believed to support a set of high-speed flaperons inboard, midspan flaps and low-speed ailerons outboard. The leading edge is made up of fixed sections inboard that appear to incorporate laminar flow treatment, while the movable devices extend from the engine nacelle to almost the wingtip.

With a gross weight of 139,000 lb., the aircraft will carry up to 70,000 lb. of fuel and a payload of 8,000 lb. As in the Concorde, the AS2 fuel system will be used to redistribute weight and balance during flight to maintain trim and compensate for changes in the center of pressure, which occurs during the transition to supersonic flight. The aircraft will feature a fly-by-wire flight control system and a 3,000-psi hydraulic system.
Aerion is offering a military AS2 derivative dubbed the High-Altitude Supercruise (HASC) platform to serve as a U.S. high-altitude surveillance and eavesdropping aircraft for the Army, Air Force and Navy. The concept includes new capabilities such as a high-altitude testbed platform for a powerful new class of high-energy lasers with power levels of 500 kW or more.